
PCB and ME30 Projects
I had taken a class in the spring 2021 where i learned how to use KiCad for the first time and got some more experience using Linux and Git for version control of projects when using ssh. As you can see, when i went to order my first PCB, my original microcontroller didn’t even fit the board!
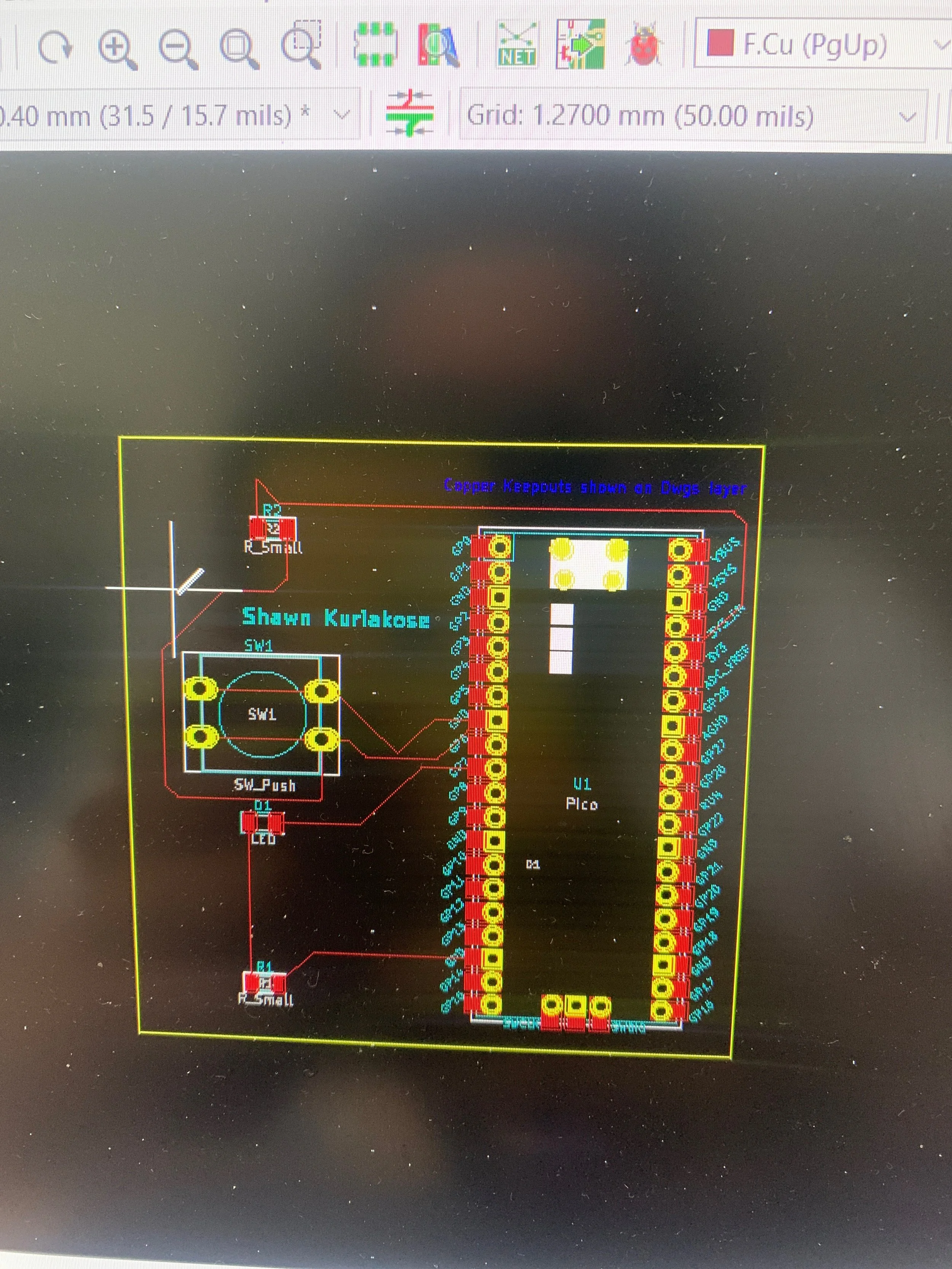

Then in the fall I took Electromechanical systems I, which is a class that further helped me to harness these techniques and work on previous acquired experience from hobby projects with other classmates.
First two projects were designs of a power supply and motor driver (L293N) in Kicad. Went through process of testing out prototype before making the design in Kicad and finally submitting the gerber files to OSHPark.
Once I recieved my PCBs in the mail, i mounted the components to make my Printed Circuit Assemblies.
Components used below:
1 3.3V Voltage Regulator
1 5V Voltage Regulator
3 10 uF Capacitors
1 Screw Terminal (1x2)
4 Pin Headers (1x2)
1 1K Ohm Resistor
1 Red LED
1 Barrel Jack Connector
1 Barrel Jack Connector
2 N-Channel MOSFETs
2 P-Channel MOSFETs
2 BJTs
1 Red LED
2 Screw Terminals (1x2)
4 Pin Headers (1x2)
3 1K Ohm Resistors
4 10K Ohm Resistors


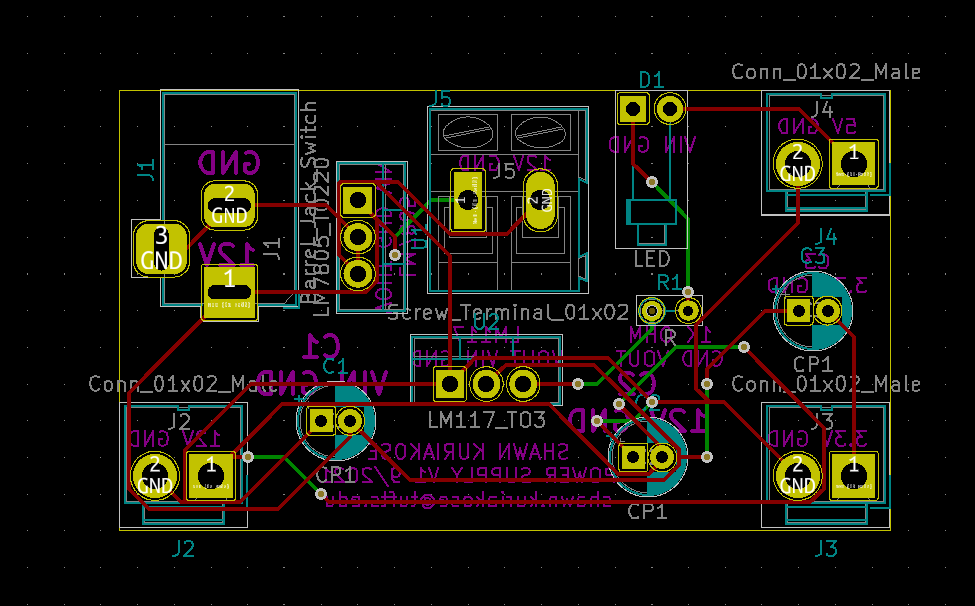

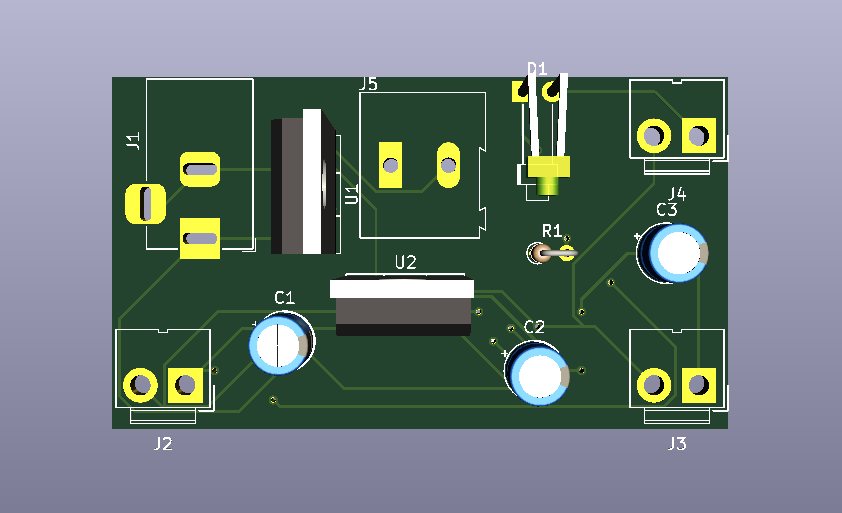
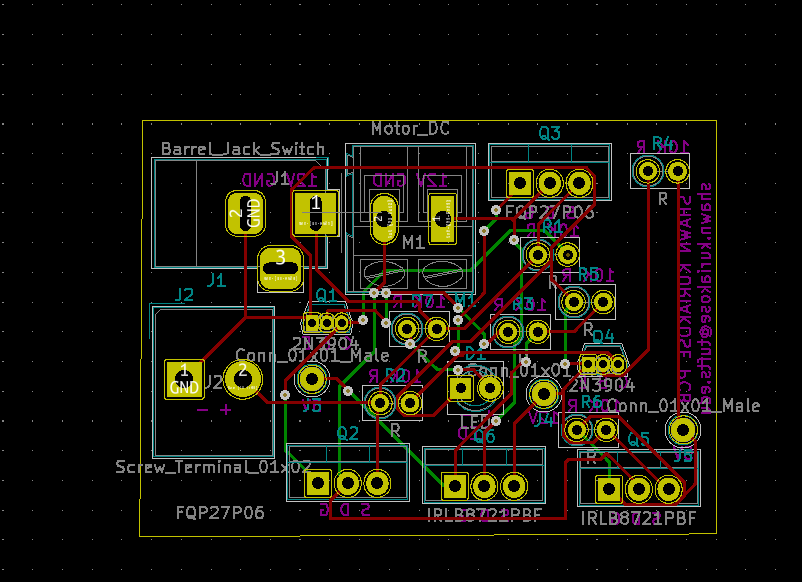
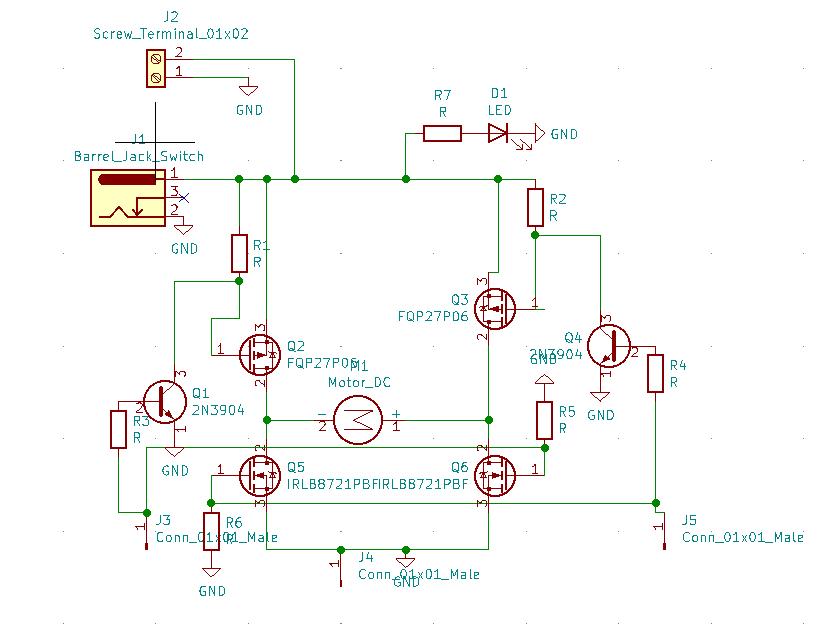

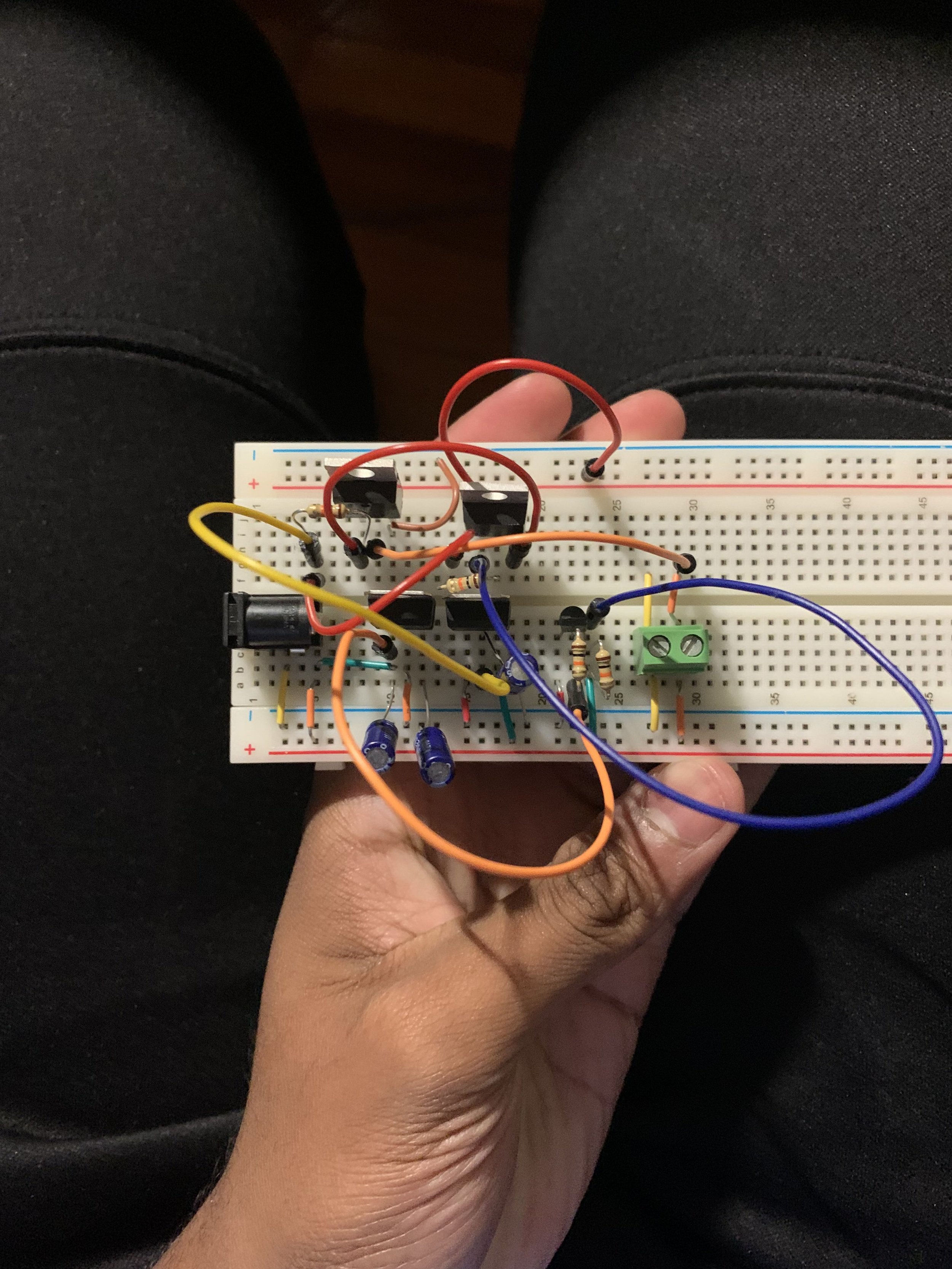
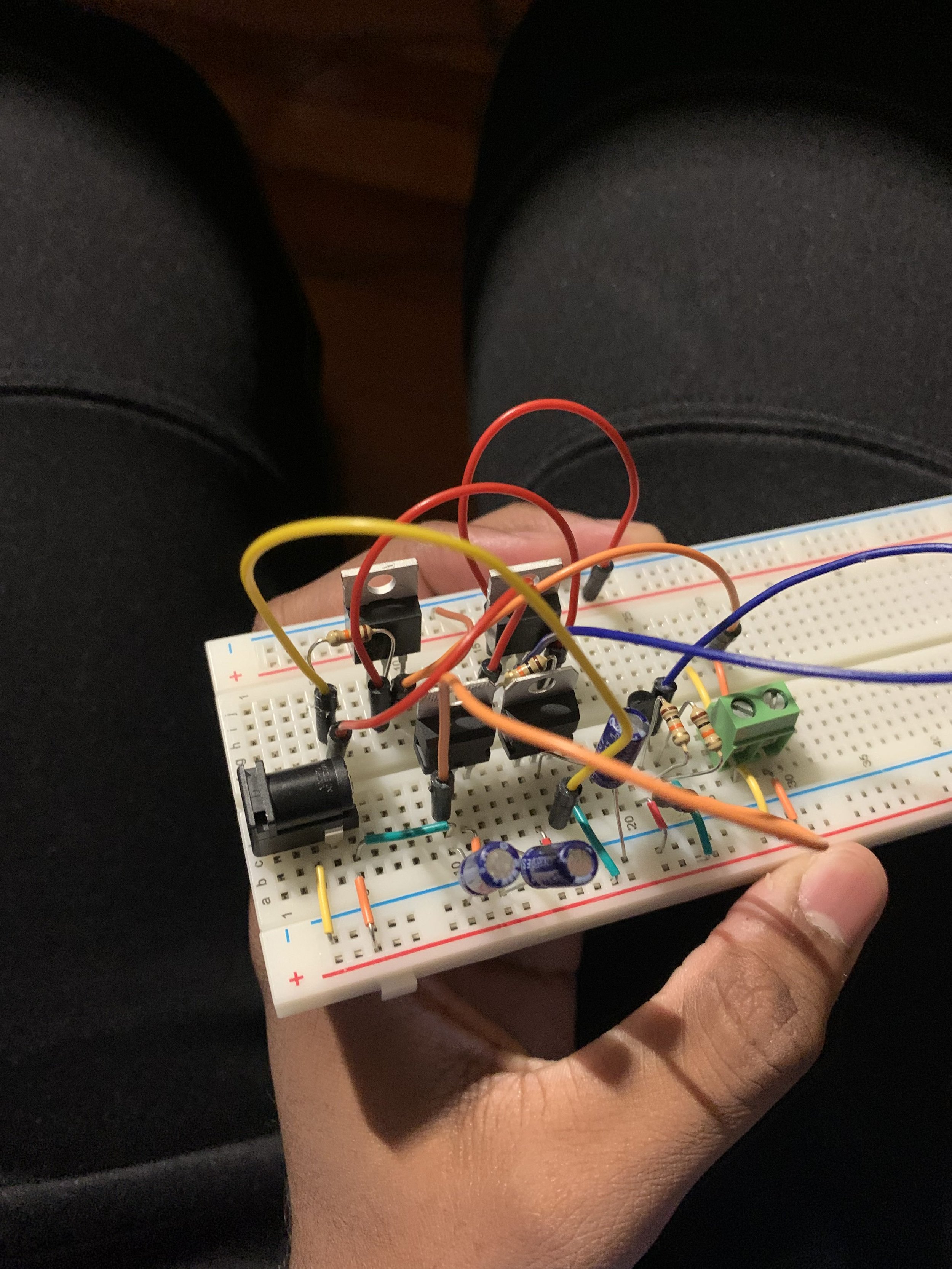
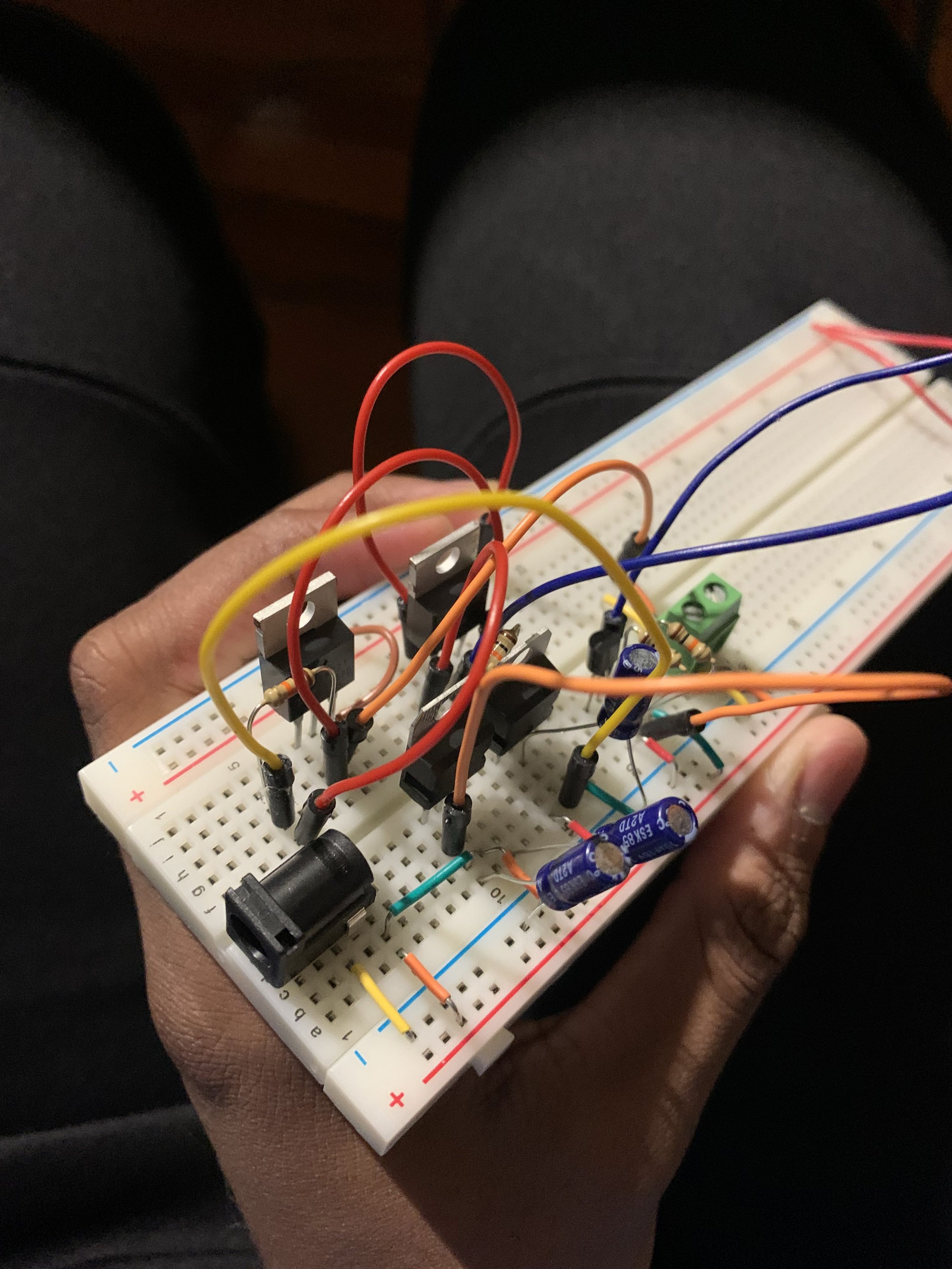
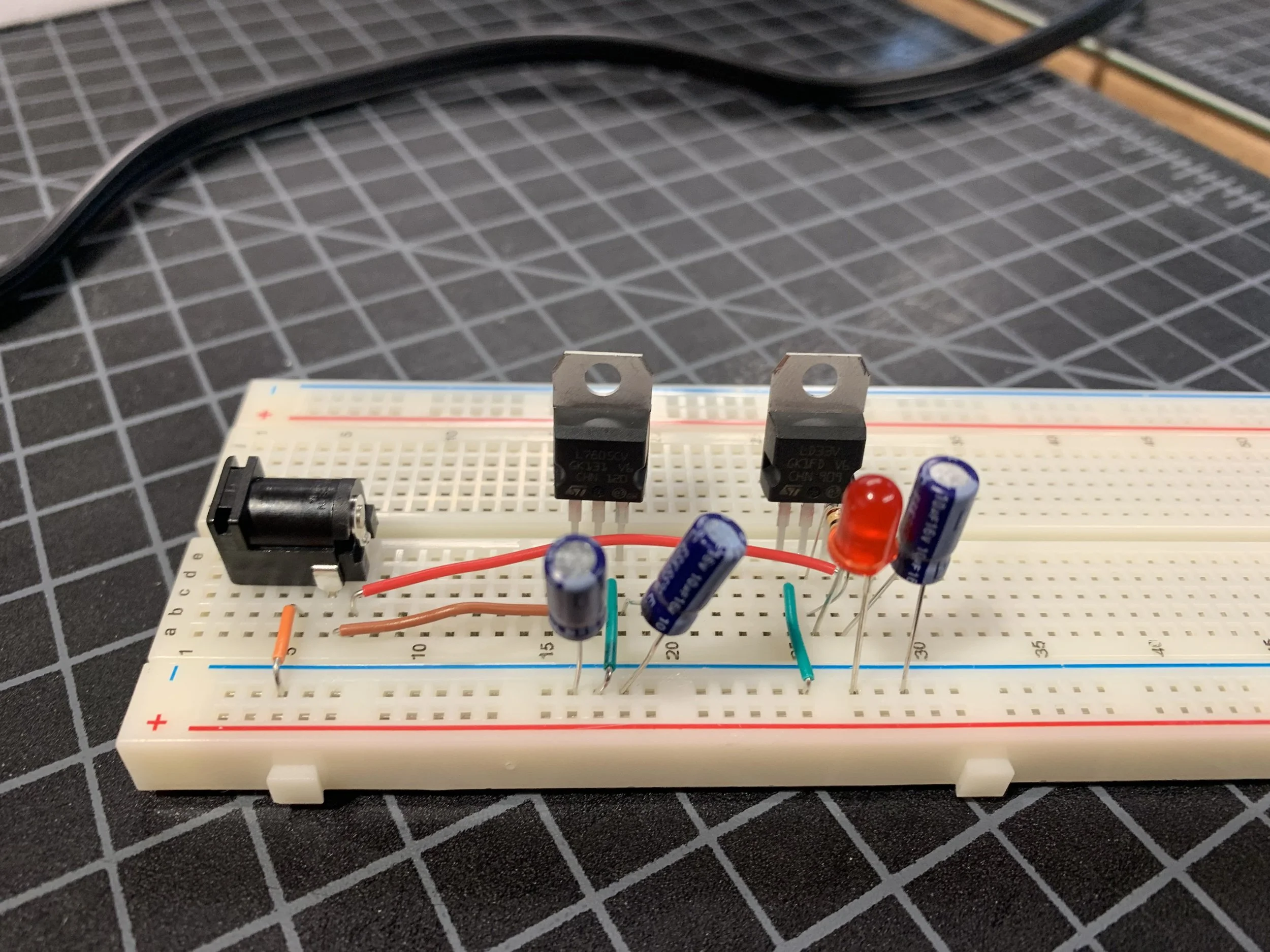
We had a project where we had to design a challenging electromechanical game. My game was called David and Goliath, a two player game where David must fill all the boxes in a board with balls before the timer expires, while Goliath at any point can dump the balls off the board.
I went through my process of prototyping the original game on breaboard with just a button, a photoresistor, and a servo motor. Then I made a full assembly in solidworks. Ultimately the biggest challenge of this project is designing a system where the servo can dump the balls of the board. This involved designing a ABS collar that could be screwed onto the servo and then be press fit onto the shaft that would be connected to the board. This project has many parts that weren’t made with the same machine, because the storage compartment could be lasercut to save time, while the game related materials have a thickness greater than the max depth for a laser cutter on campus.
What I learned from this was that everything would be bound to fail. I had a LCD display screen that broke the day of presenting to the class unexpectedly. The shaft would actually wear out the collar after signficiant use, and the servo would just fail to dump the balls of the board. This was still, a great experience to use the experience I’ve accumulated up to this point to make a very advanced and unexpected game!
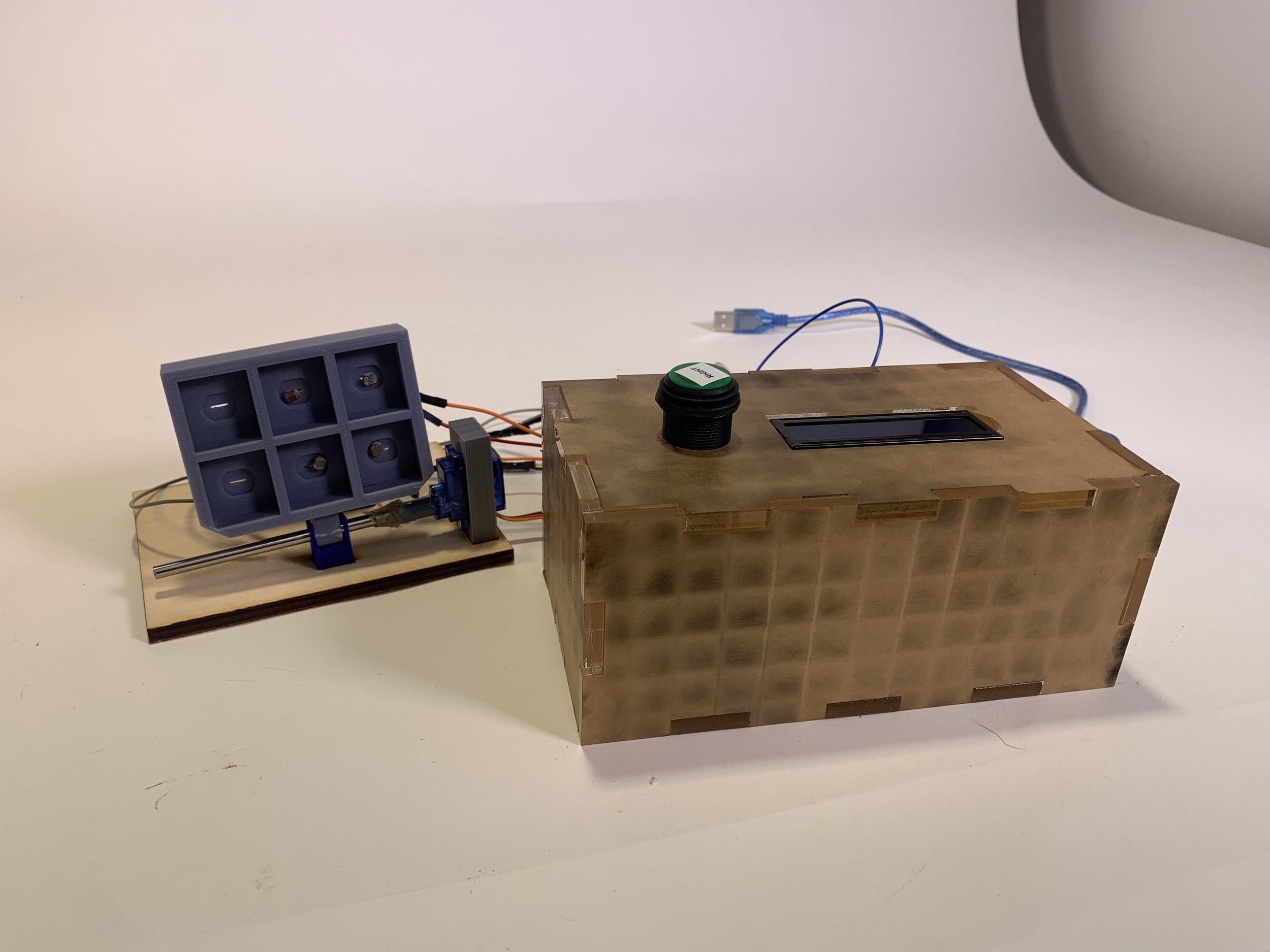
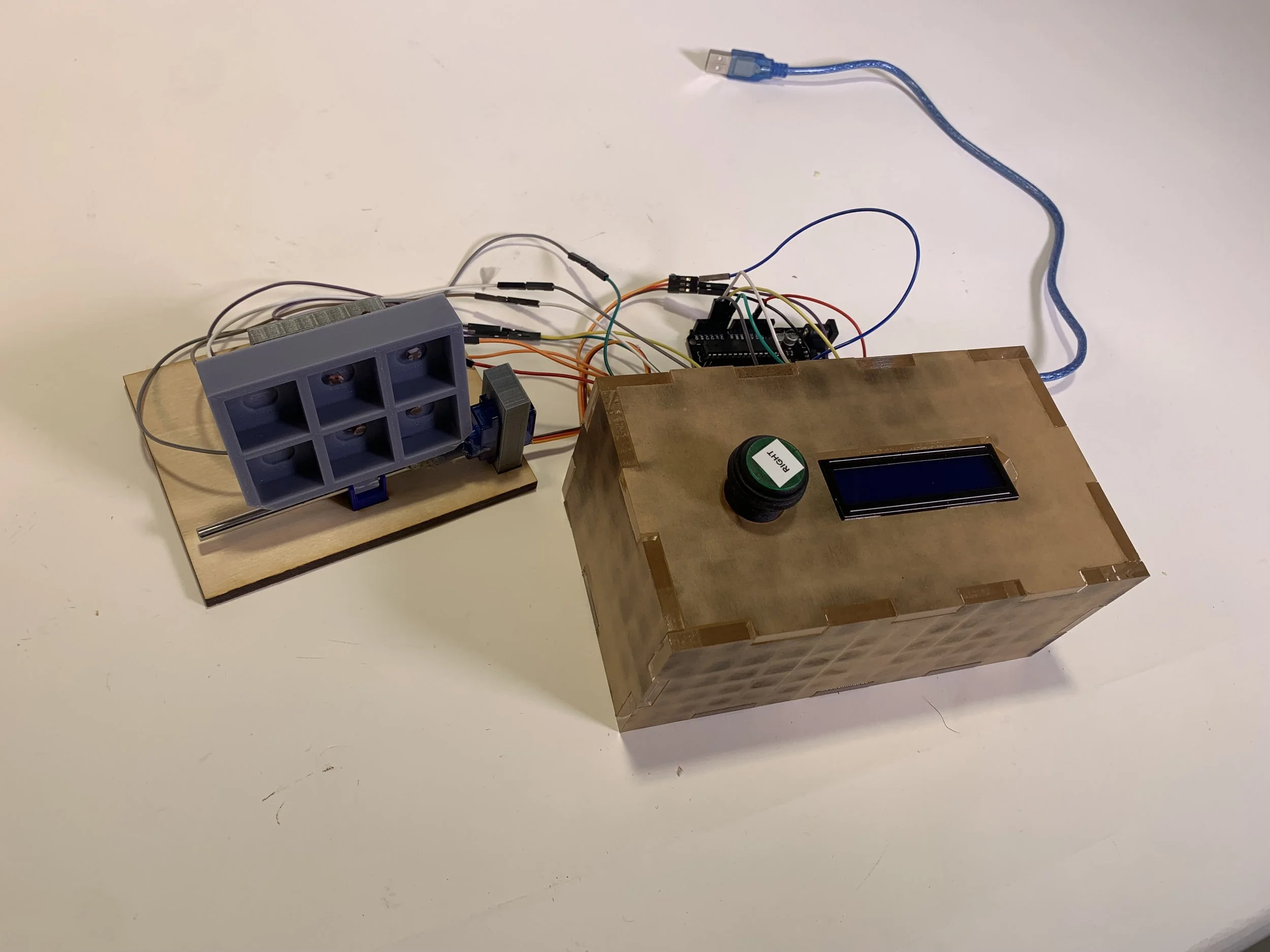
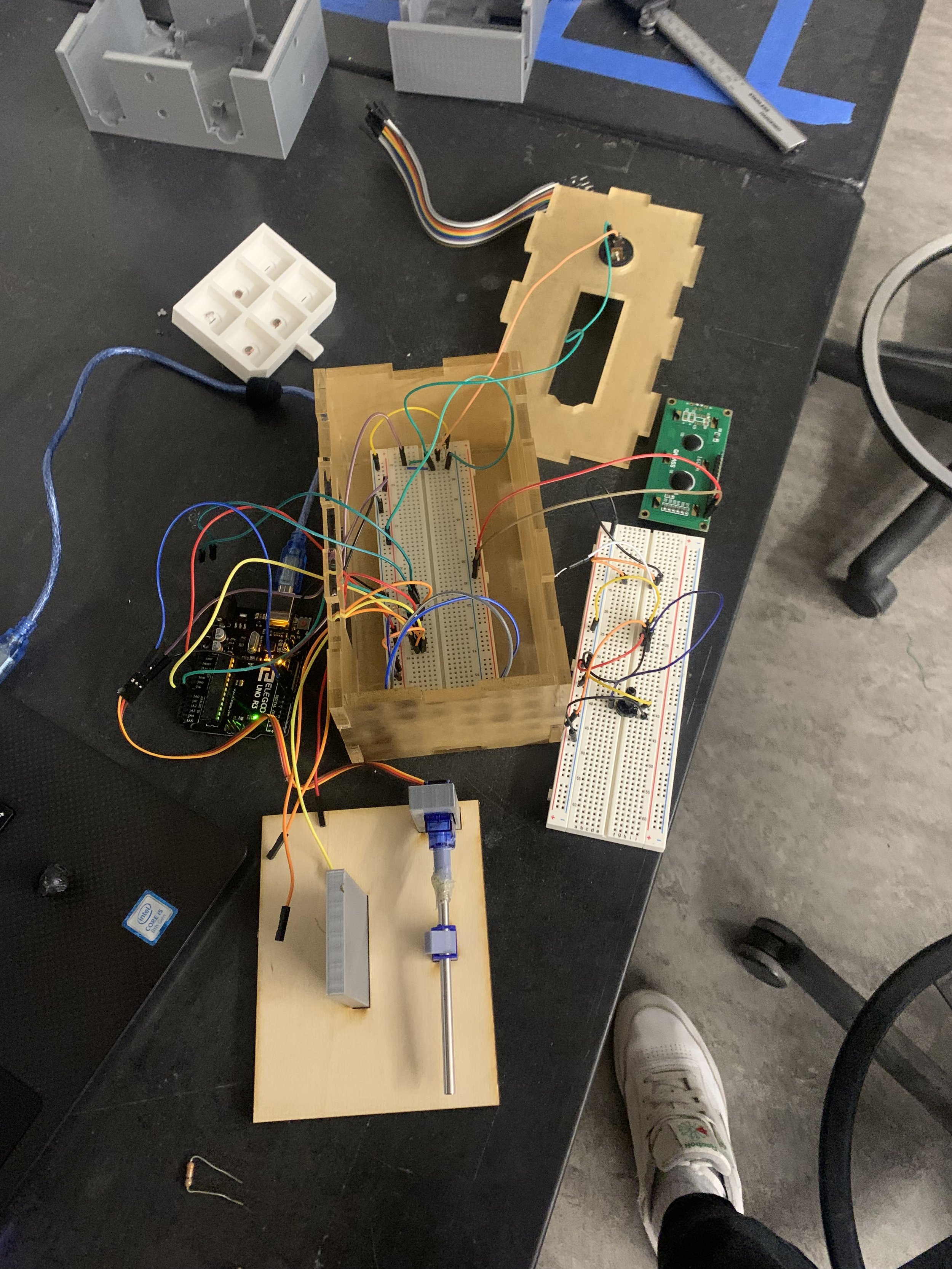
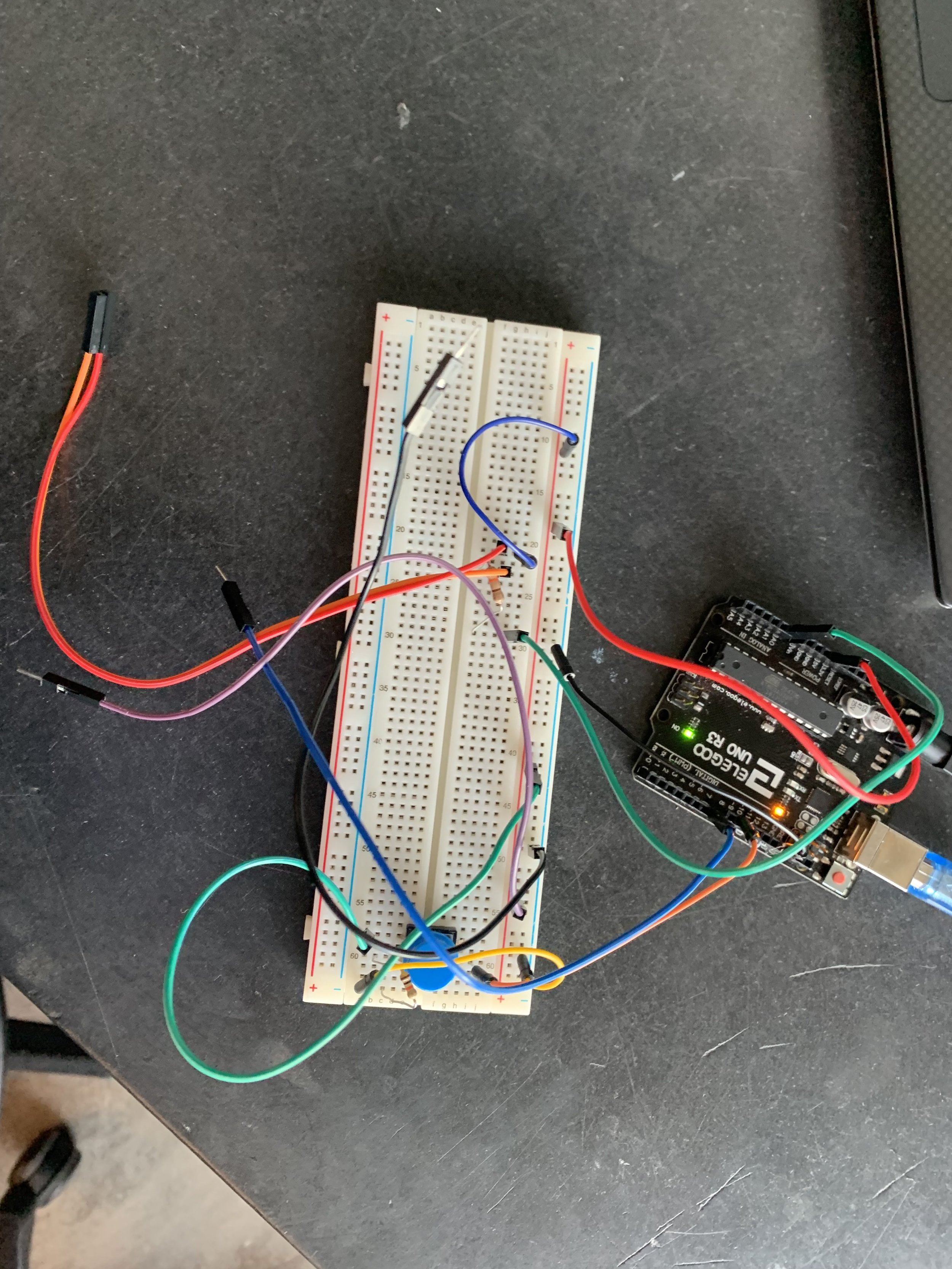