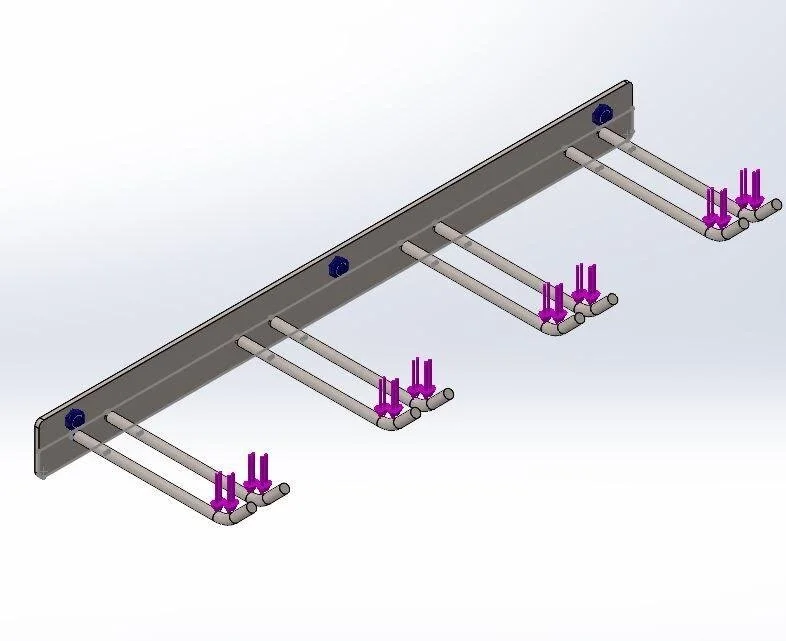
ME 10 FEA
For my sophomore materials and manufacturing class, my friend evan ensslin and I were tasked with recreating a coat rack in Solidworks and perform basic FEA analysis on the rack using our knowledge acquired during the semester. The goal was to use FEA to predict how the rack would react to real life forces, specifically where it would experience stress based on different forces and torques applied to it.
The initial stages of creating the cad model started with the decision to make a single hanger and back piece as separate components, and then use these parts to make the final rack assembly. The dimensions given to us to design the rack were 36 inches for the length of the back, 3 inches for the height of the back. We were given additional dimensions for spacing between hangers, as shown below. Assumptions regarding the hanger that were made were the diameter of the hangers being 0.5 inches. We also assumed dimensions for the bolts to be ΒΌβ in diameter.
For the FEA analysis, we first chose Alloy steel as the material for the rack based on the description of Amazon of the rack. We created a virtual wall, and 3 foundational bolts as our fixtures to simulate the rack being bolted to a wall. Then we created a force of 200lb split evenly among the eight hangers , specifically placing the forces on the tips of the hangers. We created a compatible mesh, so that if there are sharp angles in our assembly, it will make sure everything seamlessly matches up, making the FEA more accurate. We set the mesh density to be in the middle of being fine and coarse
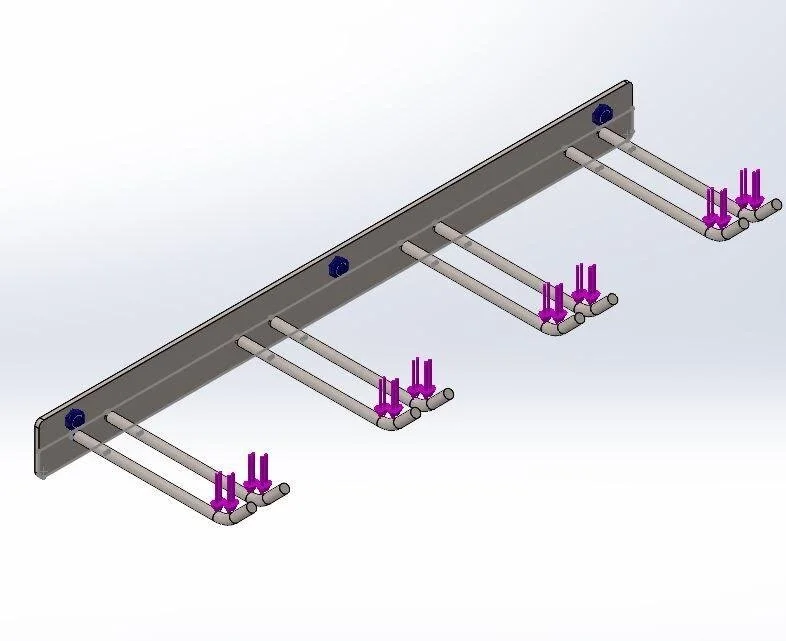

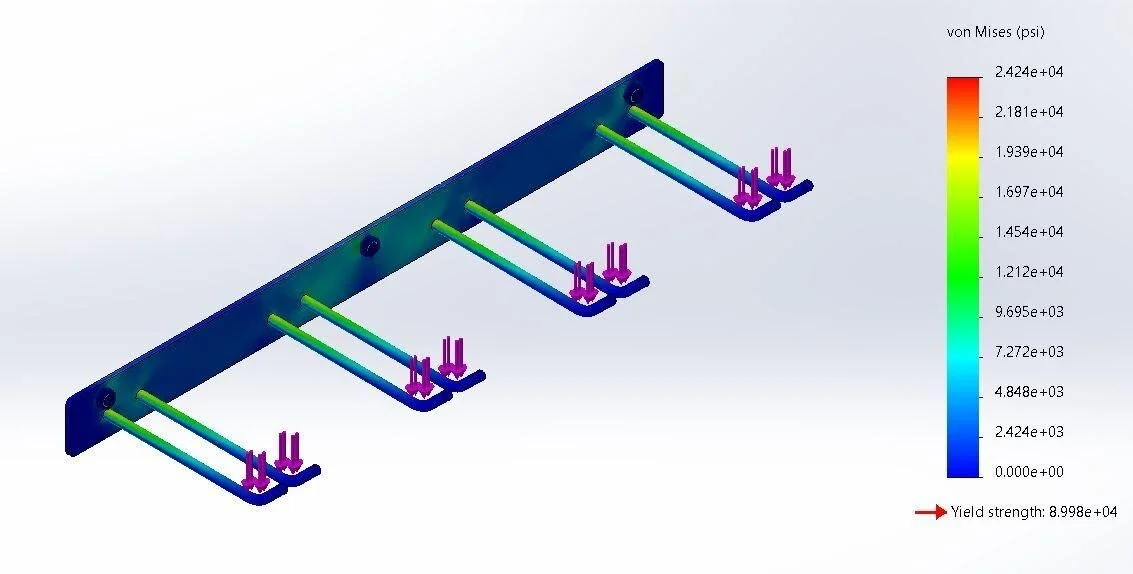
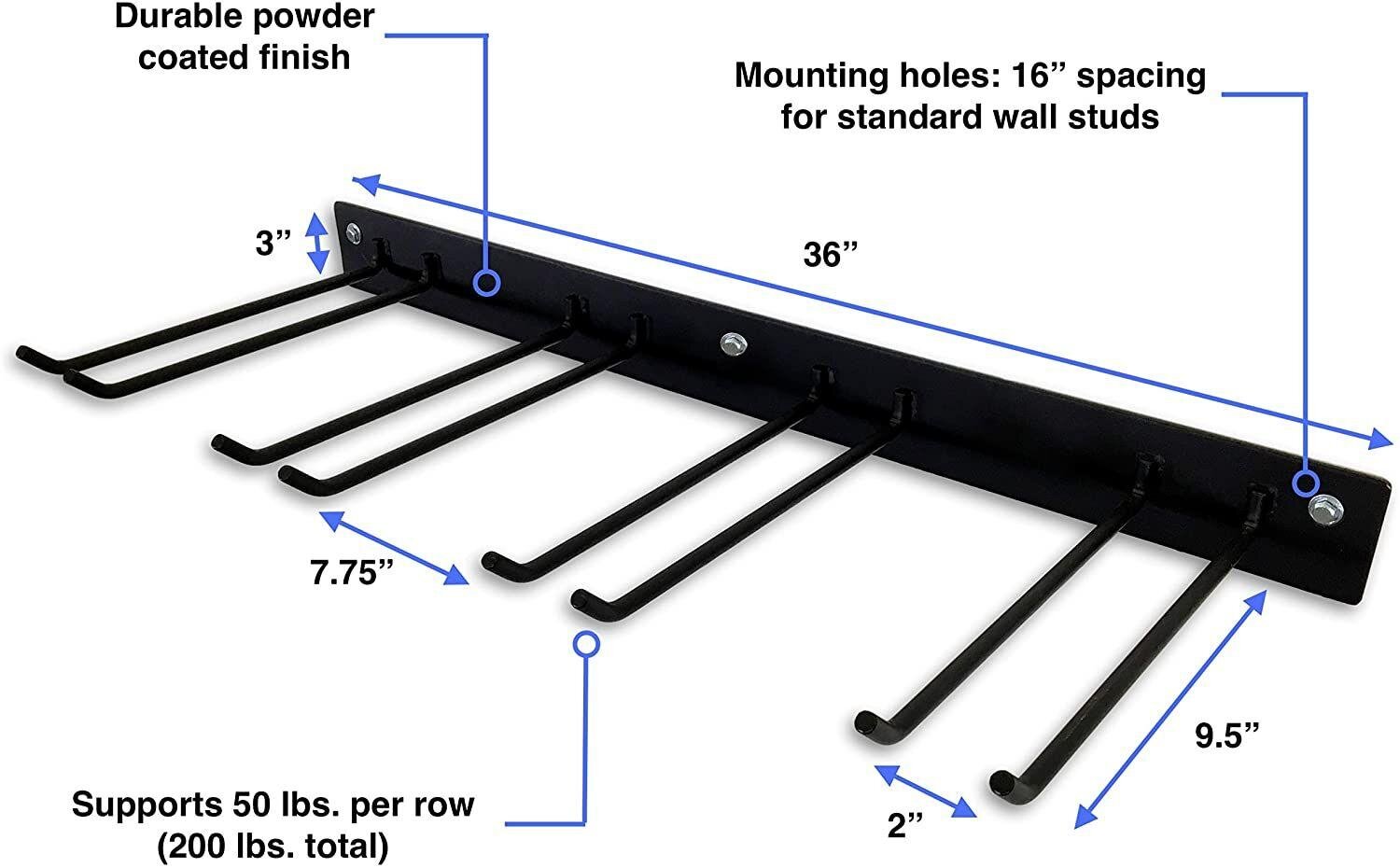